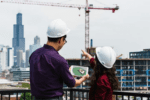
Make Better CapEx and OpEx Decisions: How Digital Twin Technology Reduces the Total Cost of Ownership
By: Anton Dy Buncio, Co-Founder & COO, VIATechnik
Let’s talk about the Chicago Bears for a minute.
In early 2024, the team proposed a new stadium that’ll cost billions of dollars to build, while taxpayers are still on the hook for 2002’s $589M investment to renovate their existing stadium, Soldier Field.
To me, this is a real-world example of a failed CapEx strategy in the Architecture, Engineering and Construction (AEC) space. Not just because of the detrimental community impact, but because somewhere along the way, there was a failure to appreciate OpEx implications in the building phase, and it led to an unfortunate CapEx decision for a new build.
“Da Bears” aren’t the only ones navigating challenging decisions around where they should be spending money to see a positive impact on their bottom line. Getting funding for any built environment project often means finding out how much money is allocated where — then doing your best to make the math work.
The status quo mindset is that building operations don’t generate revenue for the business. But what would it look like to view the balance between CapEx and OpEx as more of a seesaw within AEC, not a “stealing Peter to pay Paul” dilemma?
Budget games feel like an inevitable first step to get a new initiative off the ground, yes, but true project ROI is linked to the asset’s total cost of ownership — something many people neglect as they make OpEx decisions.
I’m writing this article so people know there’s a way to put an end to budget games with Digital Twin technology. It’s possible to connect the dots between your CapEx vs. OpEx budgets to calculate what really makes the most sense long-term. Time and time again, I’ve watched the layering of Digital Twins on top of BIM open doors to better decision-making and extended financial runways.
To understand your total cost of ownership, whether you work on the CapEx side of the house, the OpEx side, or both, you need Digital Twin technology. Here, I’ll explain how to optimize your thinking around budget and reap tangible ROI benefits.
Why No One Wins Short-Sighted CapEx/OpEx Budget Games
But here’s the problem: Short-term budget tradeoffs hurt long-term capital project investments.
For instance, if you purchase cheaper equipment to stay within budget today, you may find yourself paying more tomorrow when you realize you need to replace failing equipment sooner than expected.
Most people understand these trade-offs, and spending decisions certainly aren’t made in a mindless vacuum. In fact, many teams think carefully about things like:
- Assets as CapEx vs. OpEx
- Leasing vs. Buying vs. Financing
- How to improve existing space and assets
- When to outsource services and maintenance contracts
While deliberating the pros and cons of each budget decision has some value, the fact remains that there’s an element of guessing and short-sightedness that doesn’t account for the complexity of the full lifecycle of a built environment.
The most successful budget decisions occur when you break down the silos between CapEx and OpEx and think about the long-range life of an asset.
Two Ways Digital Twin Technology Puts an End to Budget Games
Thanks to new technology, it’s possible to make decisions that go beyond the individual bandwidth of human contributors. Digital Twins strategically process data, trends, and patterns at scale.
In other words, it thinks with you, providing a single source of truth and contextual information for every decision across your assets.
Construction is short, and a building’s lifespan is long. For example in the healthcare space, OpEx spending sometimes outpaces construction spend by 9x after just two decades have gone by. Small decisions add up, and Digital Twins bring data to the table in a way owner teams alone simply can’t.
Here are the two things I appreciate most about what Digital Twins offer:
1. Data That Sheds Light on the True Total Cost of Ownership
To clarify, a Digital Twin is simply a digital representation of a physical environment. It’s a system designed to collect information on building operations and bridge the gap between the digital and physical world.
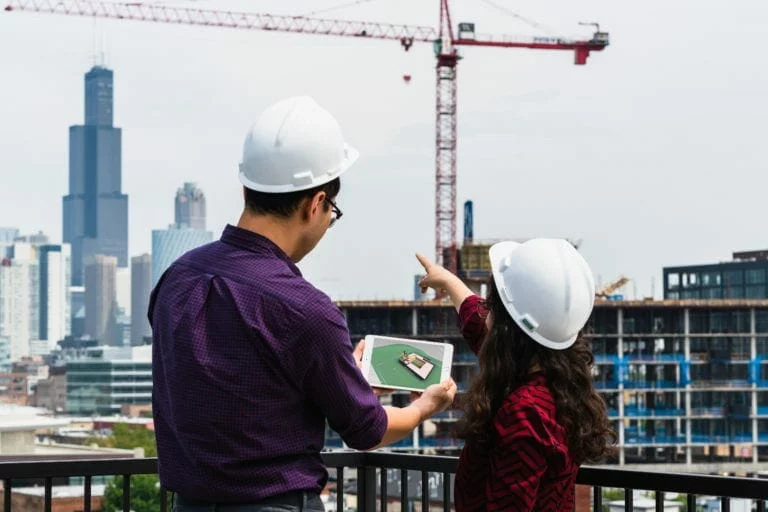
There’s a natural progression of adopting Digital Twin technology, so every organization exists along a maturity curve. It’s okay to start at the beginning and make progress with time as long as you’re using Digital Twins technology for what it was made for:
1. Understanding the total cost of built asset ownership
2. Enabling actions that minimize total cost of ownership
At VIATechnik, we help our clients approach this the right way, whether they’re just getting started or ready to fully implement a Digital Twin system, like our leading Voyager platform. No one likes a sneaky sales pitch, so I’ll spare you, but know this: CapEx and OpEx leaders alike can often benefit from having a strategic partner in this process. You want to work with someone who can guide you in making short-term decisions that’ll have a positive long-term return.
For example, Northwell Health wanted to create a digitally advanced 200,000-square-foot state-of-the-art outpatient facility with us. They knew that to build and operate this facility effectively, they’d need visibility into the building’s long-term operating costs, providing insight into both construction options now and potential facility choke points in the future.
When stakeholders across the building lifecycle fed data into their Digital Twin, they could quickly locate information, identify patterns, and make data-backed decisions to control CapEx costs.
2. Data That Enables Better Decision-Making Across an Asset’s Lifecycle
Better decisions start with better understanding. To fully grasp the total cost of ownership, you’ll want to fuel your Digital Twin with information like:
- The original purchase price of the asset
- The cost of operating the asset (both maintenance and overhead cost)
- The estimated remaining lifespan of the asset
Most importantly, you’ll need to make sure this information is visible to everyone and anyone working on the asset — adding critical transparency across CapEx and OpEx teams. With all asset data visible in a comprehensive shared location, owners’ teams begin to:
- Identify past mistakes
- Implement cost savings measures for operations
- Create frameworks for solving long-term problems
Said differently, Digital Twin technology quickly reveals how much money you’re leaving on the table when you view either OpEx or CapEx investments as more important than one another.
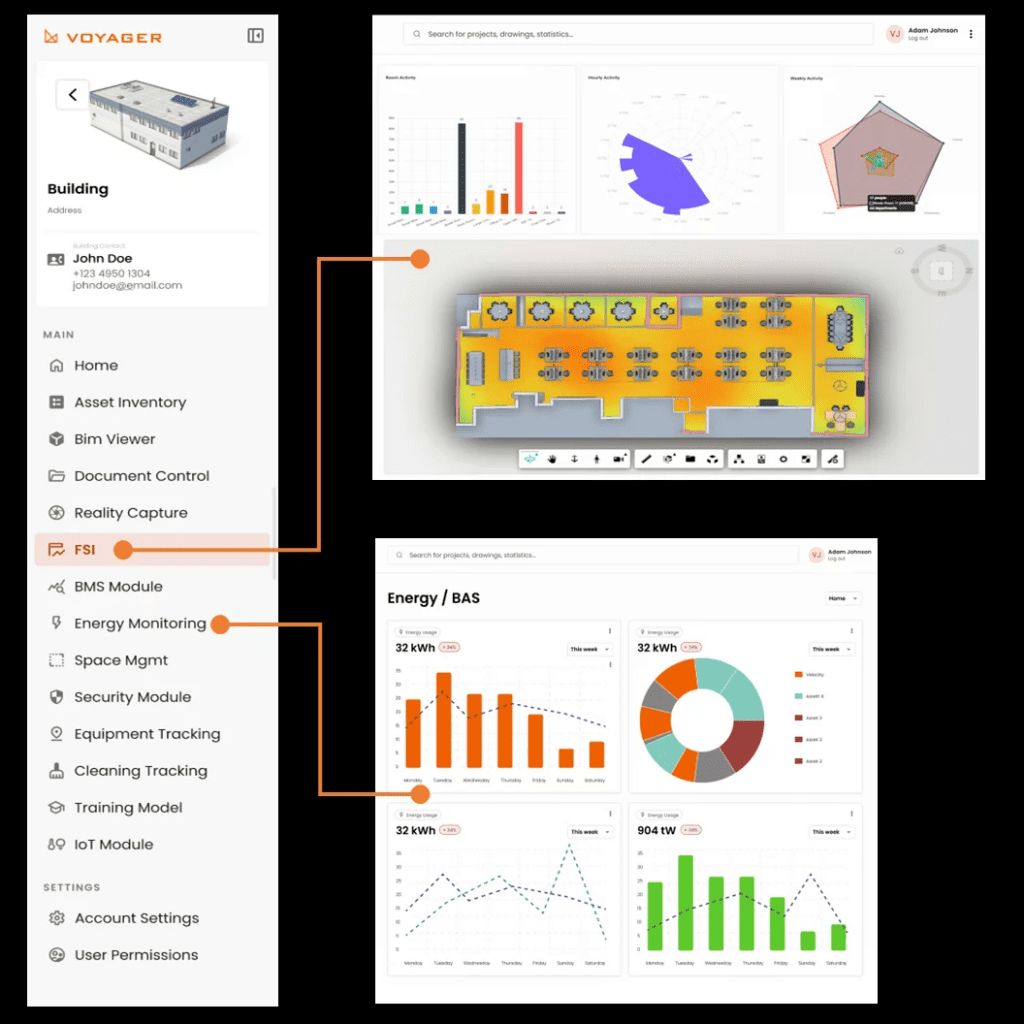
Consider how heavily Apple relies on its R&D and production teams. These departments aren’t viewed as revenue-draining engines, but rather revenue-generating ones. Their world-class ideas and manufacturing processes alike present opportunities to make money; if the R&D team can’t produce great work with their budget, the company as a whole suffers long-term.
Technological innovation is, of course, different from building management, but this same logic applies. CapEx and OpEx sit on opposite ends of a big seesaw, where you’re constantly asking questions like, “How much money should I be willing to pay for a new facilities group?” or “Would a big renovation next year enhance the value or extend the useful life of this built asset?” Digital Twin technology makes answering these questions infinitely easier and connects the dots, which is what I’ll dig into next.
Connecting the Dots: Why Digital Twins Lead to Smarter Investments that Impact OpEx Efficiency
When every decision is an informed decision, you make powerful choices that improve the function of CapEx and OpEx. Plus, you can make a positive, compounding impact on your company’s overall income. It’s amazing how many people make decisions for such little things in the CapEx budget that then go on to affect OpEx for the next 25 years.
Digital Twin technology makes gut decisions a thing of the past and offers swift answers to strategic questions — which, in turn, guides smart investments around everything from space planning to sustainability.
With long-range planning in mind and Digital Twin technology at your fingertips, you begin to make meaningful strides toward improved total cost of ownership in the following areas:
Facility Utilization
The more data you collect and feed into your Digital Twin, the more you will know about:
- The spaces and systems available in your existing buildings
- The ways that those existing spaces are currently used — or not used
For instance, at the onset of the pandemic, many owners in healthcare were caught without access to vital facility data, such as the number of hospital rooms suitable to house COVID-19 patients.
Concrete knowledge of square footage and available space isn’t just valuable during emergencies, but during routine planning and forecasting — and Digital Twin technology provides a centralized way for everyone to know in real-time what’s happening in the built environment.
The data you collect with a Digital Twin can also illustrate how users and employees interact with your existing spaces, providing clear direction for how to tackle future projects.
Future-Proofing Facilities
Digital Twin technology improves agility and adaptability as your personnel needs change, too. This is something the AEC industry consistently struggles with.
For instance, if you know your company’s overall business strategy will require your team to double in size in the years ahead, ensure that tie-in points for building system expansion are incorporated into your building or renovation plan so that you can grow down the road with fewer headaches.
Tie-in points and utility locations (including those invisible underground) can be captured using Digital Twin technology and easily referred to when the time does come for an expansion.
Sustainability and ESG
The focus on sustainability is only growing, and Digital Twin technology provides ways to assess energy usage and emissions quickly.
When you involve sustainability professionals early on, you can set initial budgets appropriately and then collect the data you need to monitor your costs and meet your company’s ESG goals.
Initial CapEx decisions that serve to lower OpEx costs over time can drive more sustainable operations, and a Digital Twin quickly pulls back the curtain on where and how you can make tweaks for the better.
Compliance
Every year, new regulatory standards push companies to provide timely compliance data to government agencies.
This is an expensive and difficult endeavor — but it becomes infinitely easier with a Digital Twin that gives people a way to better understand their built assets and comply quickly.
Start Small and Scale Based on ROI
While the benefits of Digital Twin technology are clear, finding the right entry point requires careful analysis.
I recommend finding an experienced BIM services partner who will work to understand your business and start small, working with you on an initial strategic consulting engagement that proves the ROI of solving a particular problem.
At VIATechnik, our experts work with customers to identify a single problem that’s unique to their business. Then, we show them the return on investment possible by introducing the correct BIM or Digital Twin platform. For instance, if you have numerous HVAC units with expensive maintenance contracts, we can calculate what savings would come from switching to more cost effective vendor agreements.
Once we tackle one problem together, we can tackle the next — and watch your total cost of ownership savings multiply over and over with each solved problem.
Want some expert input on balancing OpEx & CapEx spend and reducing your long-term costs? Contact us today.