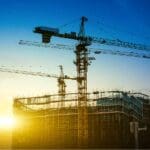
Constructing the World’s First 3D Printed Apartment Building
Exciting innovations in 3D printing is starting to change the way business is done in all sorts of industries – from medical devices to auto parts and even fashion. Engineers have been looking to 3D printing to revolutionize construction materials and techniques for several years now. A Chinese company, WinSun, has even recently completed its first 3D-printed apartment building – a five-story, 11,840-square-foot villa at Suzhou Industrial Park.
The WinSun 3D Apartment Building
A 3D printing inventor, Ma Yihe, developed the printer that created this building, and the printer stands 20 feet high by 33 feet wide by 132 feet long in size. According to CNET, the company assembles structures onsite, with steel reinforcements and insulation to comply with official building standards. The printer uses a CAD design as a template and prints the walls hollow with an internal zigzag pattern to leave room for insulation and for reinforcement.
Strength of 3D-Printed Materials
Many people entrenched in the traditional construction industry are concerned about the strength and stability of 3D-printed materials. However, site testing has shown that some types of 3D printed materials are actually better suited to extreme weather and environmental conditions. For example, curved walls can withstand earthquakes better than standard straight walls, and even straight 3D printed walls typically fare better than most traditionally-built walls today.
Budget-Friendly Designs
Although 3D printers can potentially make many different shapes and sizes, engineers on a budget are sticking to basic designs that get the job done at a minimal cost.
“Architects are crazy about those exotic designs, but they are expensive to do,” said Berok Khoshnevis, a University of Southern California engineering professor and director of the Center for Rapid Automated Fabrication Technologies. “To the printer, the task is not harder or easier.” Using CAD/CAM, the architect can make structures that are as swervy, complicated, and structurally sound as any structure in history.
Speed and Efficiency
Another perk to 3D building is the speed and efficiency with which construction could soon be completed. If building materials can be printed and organized in advance, then the actual construction time would be greatly reduced. For example, Kohshnevis says that he’s developed a process that can build a 2,500-square-foot home within a mere 20 hours. Most residential and commercial consumers don’t need this extreme level of building speed; however, this type of process could certainly be useful in emergency situations and natural disaster sites.
Overall Cost Savings
Although 3D printing is still a fairly expensive option for the construction industry, at least in terms of upfront investment, there are a few long-term benefits to consider. With these promises of speed and efficiency, the cost of labor would be greatly reduced and very few materials would go to waste.
In WinSun’s apartment building, for example, the 3D printing process saved between 30 to 60 percent of construction waste, decreased production time by 50 to 70 percent, and reduced labor costs by 50 to 80 percent. Construction of the total apartment building cost just $161,000.